Hey Folks,
After 16 years in Germany, work has planted me back in the US, for the near future at least, in State College, PA. Since my whole system was setup for 240v power I've had to convert and repackage the amps and wireless. Since three phase power seems to be nonexistent in any of the venues I'm likely to work in, I've had to take a wholesale step backwards and build a poorman's distro and get a bunch of Edison extension cables. And no, they're not yellow. So far so good, although I miss those really slick three phase CEE connectors already.
While tinkering with the problem of how to rerack everything I started looking at case manufacturers in the US and realized that none of them seem to use extruded aluminum rack rails, only the predrilled/tapped steel angle. Is this normal? In most of Europe, only the cheapest cases have the steel pretapped stuff. Everything from Bargain Basement on up uses extruded aluminum which give you a lot more flexibility with equipment location, is stronger and uses a larger 5mm screw with a nice broad head. Is it normal even at the pro level in the US to use racks with predrilled and tapped steel rack rails?
Here is a picture of the extruded rack rail I'm talking about.
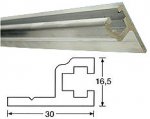
Ciao
Simon
After 16 years in Germany, work has planted me back in the US, for the near future at least, in State College, PA. Since my whole system was setup for 240v power I've had to convert and repackage the amps and wireless. Since three phase power seems to be nonexistent in any of the venues I'm likely to work in, I've had to take a wholesale step backwards and build a poorman's distro and get a bunch of Edison extension cables. And no, they're not yellow. So far so good, although I miss those really slick three phase CEE connectors already.
While tinkering with the problem of how to rerack everything I started looking at case manufacturers in the US and realized that none of them seem to use extruded aluminum rack rails, only the predrilled/tapped steel angle. Is this normal? In most of Europe, only the cheapest cases have the steel pretapped stuff. Everything from Bargain Basement on up uses extruded aluminum which give you a lot more flexibility with equipment location, is stronger and uses a larger 5mm screw with a nice broad head. Is it normal even at the pro level in the US to use racks with predrilled and tapped steel rack rails?
Here is a picture of the extruded rack rail I'm talking about.
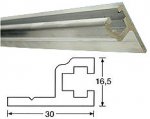
Ciao
Simon