Re: 60 Degree DIY Mid Hi
So I've been doing a lot of modeling in Inventor, and I pretty much have the cabinet done. I won't say anything just yet - first, a quick picture:
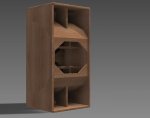
Parts haven't come yet, but here are some noteworthy parts of this box:
Depending on how this goes and if Peter gives me the green light, I will post a link to the files, as well as just generic drawings for those who aren't as CAD inclined. I haven't added handles, and the internal bracing has not be finalized either. I get the ply in on Wednesday, but I plan to start testing the CNC process with less fantastic wood tomorrow - with any luck it will all fit on one 4'x8' sheet of ply. If not - whatever. I've got extra space when the BB comes along.
One last thing - I've always wanted to do this~!:
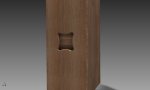
So I've been doing a lot of modeling in Inventor, and I pretty much have the cabinet done. I won't say anything just yet - first, a quick picture:
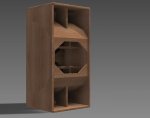
Parts haven't come yet, but here are some noteworthy parts of this box:
- First and foremost, I will be creating as many of the parts as possible on a ShopBot 4'x8' machine. Part of this is because Helge said he wanted to use a CNC shop, and I wanted to make sure all of the parts were possible. The other reason is that I just want to.
- Second, the box does not have interchangeable horn baffles. I decided that, although it's possible, I simply did not want to deal with making the parts. Which is ironic, considering...
- I added a maintenance panel to the left side of the box (a la DSL). It will be secured using T-nuts and machine screws, and will have a gasket. This is completely optional, and can be replaced with the same model from the other side.
- The box is wider than other models to allow for a full front grille. It's my box - I'll do what I want! 8)~
~
Depending on how this goes and if Peter gives me the green light, I will post a link to the files, as well as just generic drawings for those who aren't as CAD inclined. I haven't added handles, and the internal bracing has not be finalized either. I get the ply in on Wednesday, but I plan to start testing the CNC process with less fantastic wood tomorrow - with any luck it will all fit on one 4'x8' sheet of ply. If not - whatever. I've got extra space when the BB comes along.
One last thing - I've always wanted to do this~!:
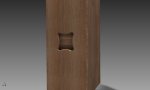